Mines alum transforming food waste into high-quality animal feed

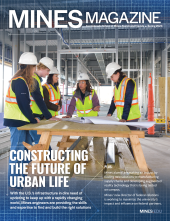
Food production is the largest source of global waste, often ending up in landfills and incinerators. Concurrently, animal feed production is the world’s most resource-intensive industry, taking up billions of acres of land. But manufacturer FeedBack Earth is working to mitigate both of these problems by turning food waste into high-quality animal feed.
FeedBack Earth—a manufacturer based in Massachusetts—takes unwanted, discarded food product and safely converts it into a high-quality, nutritional feed that farmers and mills in the New England-area can use to feed their livestock. And at every point in the process, FeedBack Earth is using sustainable practices, from transforming the economics and environmental footprint of the industry to ensuring their operation is mindful of their impact on local communities.
We talked to Eric DePinto ’13, director of operations and engineering at FeedBack Earth, to learn more about how the company is shaking up the traditional animal feed supply chain with sustainability and value in mind.
What makes FeedBack Earth unique in the manufacturing industry, specifically when it comes to producing high-quality animal feed?
Eric DePinto: We’re not the first company to do something like this, but our technology is a bit more unique. The waste industry is historically non-technological, and it’s rooted in established traditions. We felt like we could take a technology that was underdeveloped and underutilized and layer on best practices in operations, manufacturing and technical ability from all our collective backgrounds and really make something that was way more efficient than anybody’s ever seen. Higher volumes than anybody’s ever seen. Create a better product than anybody’s ever seen. And we felt that could be scaled into not just siloed little companies but this big corporation that can expand nationally and globally to build something that has a great impact.
What has been the customer and industry response to your product and process?
DePinto: We have customers on both ends. The customers on the final animal-feed product end love it. They love the consistency in both appearance and nutrition. Competitors in the region that apply a similar technology tend to have less control over nutrition and how the final product looks. We’ve been able to develop something that’s nutritionally consistent and visually consistent, which has a lot of appeal for the farmers and mills that feed it or blend it for their animals.
On the other end of the customer side, we have the food manufacturing facilities that generate waste product. A lot of them never had the option of bringing it to a facility that sustainably reuses it. They were often giving it away for free to farmers out the back door or sending it to a landfill.
We really pride ourselves in offering a one-stop shop to handle all food waste from the facility and being able to bring that into our facility and create an end-product that has a ton of appeal to customers on both sides.
How does your process differ from conventional methods of creating animal feed?
DePinto: A lot of places don’t actually cook the material. They will take it in—and they have a very narrow range of what they can take in—and then they will de-package it, grind it up and feed it directly to the animal. Our process is unique in that we can take in a much wider array of materials. We have the ability to handle select types of meat as well because we pasteurize the material and then we dehydrate it. That gives it a longer shelf life, and that gives us a broader spectrum of what we can take in, and
we can have the biggest impact.
How do you ensure you’re remaining competitive with conventional methods while producing a high-quality product?
DePinto: No business is going to be successful if the bottom line doesn’t work, right? We try to have tight control over the cost of goods that we have to put into the product, whether that’s labor, energy, cost of material acquisition, trucking. There’s a ton of components that go into getting and processing the material. And then like a lot of manufacturing, we are subject to a commodities market. We’re always trying to be efficient with what we have to put into the product to get the same product out.
How Feedback Earth’s process works

- FeedBack Earth supplies enclosed dumpsters and trailers to some of the largest manufacturers of products such as frozen breaded fish and fast-food hamburger buns. These manufacturers have a 10–20-ton-per-day waste stream that gets collected and brought back to the FeedBack Earth facility.
- That food waste is processed through a de-packaging machine, sent through a massive shredder and gets roughly sorted by nutritional “likeness.”
- The material is then homogenized further to reach a desired nutrition level before it’s sent into a fluidized bed dryer that cooks and dehydrates the product from about a 40 percent moisture level to around a 10 percent finished moisture level.
- The product is ground into a fine grain-like feed and is screened out for any remaining trash and passed through a magnet to remove any metal.
- The resulting product is packaged and loaded into trucks that take 20 to 30 tons of feed at a time to a farm or mill in New England.
Learn more about FeedBack Earth at feedback.earth.