Mines researcher contributing to $4M DOE project for energy-efficient steelmaking
Steelmaking is among the most energy- and carbon-dioxide-intensive process in manufacturing. U.S. steel producers are challenged by narrow profit margins due to the cost of raw materials and associated energy costs.
But researchers at Missouri University of Science and Technology and Colorado School of Mines could soon help the steel industry overcome those challenges.
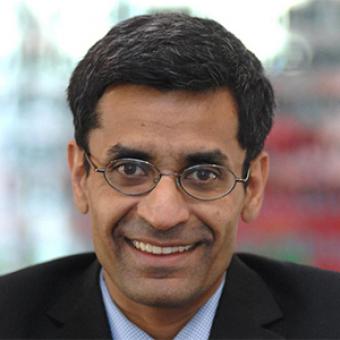
With a $4 million grant from the U.S. Department of Energy, Mines’ Sridhar Seetharaman and Missouri S&T’s Ronald O’Malley are working to prove the economic viability of increased renewable energy usage in steel production.
The project would create a steel production system that combines a hydrogen-reduction reactor for ironmaking (H2DR) with electric furnace melting for steelmaking. This combination is then integrated into a flexible electrical grid with energy storage and hydrogen generation by balancing hydrogen and natural gas usage in the H2DR process.
O’Malley and Seetharaman, associate vice president of research and professor of metallurgical and materials engineering at Mines, believe that the increased integration of electric power for steelmaking using electrolysis will help balance the electrical grid and reduce carbon dioxide emissions.
“The integration of this H2DR combination into the U.S. supply chain would be a proof-of-concept that the steel industry is ready for de-carbonization,” says O’Malley, the F. Kenneth Iverson Endowed Chair of Steelmaking Technologies and director of the Kent D. Peaslee Steel Manufacturing Research Center at Missouri S&T.
The researchers believe that de-carbonization of the steel industry can be achieved by connecting ironmaking to renewable electric power through electrolytically produced hydrogen.
“While the use of hydrogen to produce iron from ore is proven, the impact of dynamically rebalanced reducing gas mixtures in the H2DR process on the steelmaking must be assessed” says O’Malley. “This requires a closure of several knowledge gaps in ironmaking and EAF steelmaking.”
The grant is part of a DOE investment of $64 million in 18 projects from the Office of Energy Efficiency and Renewable Energy’s Hydrogen and Fuel Cell Technologies Office to support affordable hydrogen production, storage, distribution and use. The projects will develop low-cost, high-strength carbon fiber for hydrogen storage tanks and identify durable and cost-effective fuel cell systems and components for medium- and heavy-duty trucks, and across industrial sectors like steelmaking.
Also partnering on the grant is the U.S. Department of Energy's National Renewable Energy Laboratory; steel supply chain representatives Danieli Corp. and Voestalpine Texas LLC; steelmakers Steel Dynamics Inc., Gerdau, and Nucor Steel; and industrial gas suppliers Praxair Inc. and Air Liquide.
“The work will strengthen Mines’ collaboration with NREL and Missouri S&T and allow all three institutions to leverage their respective strengths towards decarbonation of the heavy industry,” Seetharaman said.
For more information about the grant, visit www.energy.gov.