Mines researchers test how 3D-printed materials perform inside a nuclear reactor
Could 3D printing, also known as additive manufacturing, solve the difficulty of finding replacement parts for nation's aging nuclear plants?
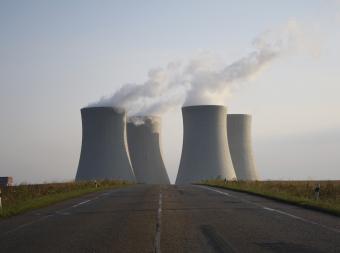
By Sarah Kuta, Special to Mines Newsroom
As our nation’s nuclear plants age, it’s becoming increasingly difficult to find replacement parts—the shapes and sizes are unique, plus they must be able to withstand a harsh, radioactive environment.
But Mines researchers are studying a novel question: could 3D printing—also known as additive manufacturing—be the solution to this problem?
The researchers, led by Jeff King, associate professor of metallurgical and materials engineering, are testing how 3D-printed materials perform in a nuclear reactor. The results of this four-year, $2.5 million study, funded by the U.S. Department of Energy, have the potential to revolutionize the nuclear power industry.
“Most of the reactors in the U.S. are more than 40 years old, and many of the companies that made the original parts no longer exist,” said King. “There’s a huge problem of trying to find replacement parts and/or certifying replacement parts. One theory is if you could make on-demand parts of specific geometries through additive manufacturing, this could be very helpful in keeping our aging nuclear fleet performing.”
In supply chain logistics more broadly, additive manufacturing is an exciting and potentially transformational technology. The process makes it easy to quickly and efficiently produce parts on demand, rather than waiting for them to be manufactured and shipped. It can also make it cheaper and easier to produce irregularly shaped components.
For the nuclear industry, the big question revolves around safety and how 3D-printed materials behave inside a nuclear reactor. The researchers want to understand whether 3D-printed materials are uniquely vulnerable to radiation damage or are, in fact, stronger and more durable than conventionally manufactured materials.
“If that’s true, then that enables things like longer lifetimes for reactors, greater efficiencies and reduced costs,” King said. “These are the sorts of things that are necessary for rolling out the next generation of nuclear reactors.”
To study this question, Mines researchers used five 3D-printing methods to create 288 samples of stainless steel and Inconel alloys. They sent the samples to the Advanced Test Reactor at the Idaho National Laboratory, where they were exposed to neutron radiation for 80 or 160 days.
With irradiation now complete and a cool-down phase underway, researchers will soon begin testing the strength and thermal properties of the samples and looking at them under an electron microscope to see what changes occurred at the microstructure level. They’ll then compare this information to data collected at Mines from irradiated samples of the same materials.
Mines is a pioneer in this complex, multifaceted line of research—in fact, it’s the first university to irradiate additively manufactured specimens in a nuclear reactor. The study wouldn’t be possible without collaboration among many departments, including metallurgy, materials science, mechanical engineering and nuclear engineering, as well as the Alliance for the Development of Additive Processing Technologies and the Nuclear Science and Engineering Center.
Though it’s still early, the researchers are hopeful about the study’s potential to advance nuclear power, one of the most sustainable and environmentally friendly energy sources available today.
Mark Graham, a graduate student working on the project, said, “If we can aid in the advancement and efficiency of this technology, we can hope to provide clean energy to everyone and reduce our predicted impact on the environment before it’s too late.”