Blasting off: Mines team tests bioreactor on weightless parabolic flights
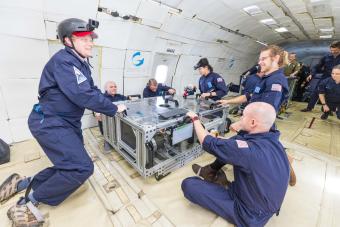
For future human-led missions to space to be successful, the ability to respond to challenges is key. If a tool breaks in space, the solution isn’t as easy as popping down to the hardware store to buy a new one. If a crew member breaks a bone and needs a cast, there isn’t an emergency room around the corner. If a space suit tears, you can’t order a new one from Amazon.
A great way to address those issues while in space is to 3D print materials on the spot. But creating the raw plastic material that would be needed to 3D print in space isn’t a straightforward process.
To move the technology forward, a group of Mines researchers have been working on a bioreactor that incorporates gas exchange technology to create plastic feedstock for 3D printing. With funding from NASA, Johan Vanneste, research associate professor in civil and environmental engineering, and Junko Munakata Marr, department head of civil and environmental engineering, are leading a team of graduate students in partnership with bioplastic producer startup Mango Materials.
While the processes that generate oxygen and methane for the bioreactor in situ — for instance, from the Martian carbon dioxide atmosphere — have been tested in space, the bioreactor and the membrane technology to get the gasses uniformly distributed in the reactor have not. Having a space-ready bioreactor that can produce bioplastic – plastic produced by microbes, which can be found in the natural environment and is biocompatible for medical applications – could greatly enhance space exploration.
“We know the bioreactor works on Earth, but it hadn’t been tested in low-gravity environments, similar to what you’d find in space,” said Alexandre Bray, a graduate student in space resources who serves as technical lead on the project.
For NASA to take the bioreactor up to space and get 3D printing going, the researchers first had to prove that its gas exchange technology is “space ready.” Bubble diffusers used in terrestrial bioreactors don't work in low-gravity environments due to bubble coalescence limiting mass transfer. Instead, hydrophobic microporous membrane contactors, which are similar to Gore-Tex, that let gases pass through and diffuse in the liquid but prevent liquid passage, were tested in low gravity.
Enter parabolic flights, which can simulate space’s low-gravity environment.
For the test flights, a team of six – Vanneste, Bray and fellow Mines graduate student Alexander Schwiebert along with three colleagues from Mango Materials – strapped the bioreactor to a plane’s floor to test how gases pass through the membrane in the bioreactor at different levels of gravity.
The team ran multiple simulations – 10 that recreated lunar gravity, 10 that recreated gravity on Mars and 10 with microgravity. In one parabolic flight after another, the team released the gas, observed how it passed through the membrane and recorded the findings. The time span for each test ranged from 15 to 30 seconds.
“We had a very short window during each parabola to capture the data,” Vanneste said. “But we were able to make it happen and record our observations.”
After comparing the results from the parabolic flights to how the bioreactor works on Earth they found no obvious difference in how the gases passed through the membrane at different gravity levels – a success. The next step? Sending the project to the ultimate zero-gravity environment – the International Space Station.
“This was the last component to validate before testing happens in space,” Bray said. “The goal is to have a full-scale bioplastic producing 3D printer in space, and we’re a step closer to that.”