Colorado School of Mines students awarded NASA research grant for megawatt-scale, high-voltage, supersonic, electric turbofan project
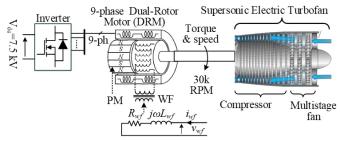
A team of students from Colorado School of Mines has been selected by NASA to participate in the University Student Research Challenge (USRC), an initiative designed to engage university teams in real-world aviation research.
The team, led by Mahzad Gholamian, a PhD candidate in Electrical Engineering, is developing a 25 MW, 7.5 kV electric turbofan system that could contribute to the electrification of supersonic commercial airplanes.
“With aviation increasingly shifting toward electrification and decarbonization, our research plays a crucial role in advancing next-generation electric propulsion systems that reduce reliance on fossil fuels and lower carbon emissions,” Gholamian said.
Current commercial flights are subsonic with airliners traveling around a speed of Mach 0.85. A standard commercial flight from New York to London takes approximately 7 hours, whereas a supersonic aircraft, traveling at speeds of over Mach 1 (and below Mach 5), could cut this time in half to just 3.5 hours. But traditional supersonic aircraft like the Concorde were phased out due to high fuel consumption, noise pollution and cost of operation while transporting a limited number of passengers.
“Our engineering perspective suggests that rather than abandoning supersonic flight due to these challenges, we should seek innovative solutions to overcome them,” Gholamian said.
By integrating a novel high-power and high-voltage electric propulsion, the team aims to enhance efficiency, reduce emissions and improve sustainability—all while making supersonic travel greener, eliminating dependence on traditional jet fuel, and paving the way for a new era of sustainable high-speed aviation.
One key challenge, Gholamian said, is the failure of power electronics components, which can compromise system performance. The Mines team’s design includes a novel dual-rotor motor (DRM) topology to enhance power-density, energy accessibility and reliability by providing redundancy in power generation—if one rotor encounters an issue, the other can continue functioning.
Additionally, its 9-phase design, compared to conventional 3-phase systems, was conceived to improve fault tolerance, ensuring continued operation even under partial failure, she said. Supersonic aircraft also require high thrust, and the team’s DRM is designed to operate at 15,000 RPM, delivering 25 MW per engine, with a mid-size supersonic plane requiring four such electric engines.
Rounding out the interdisciplinary team are Garret Reader, an undergraduate student in Electrical Engineering in charge of prototyping and testing, including fabricating an initial 3D printed model of the DRM; Henri Phillips, an undergraduate student Mechanical Engineering in charge of the mechanical design of the engine, including fan and compressor stages; and Mirali Seyedrezaei, a PhD student in Mineral and Energy Economics in charge of the project’s crowdfunding campaign. The team is being guided by Omid Beik, assistant professor of electrical engineering, an expert in electric propulsion systems.
Through USRC, students are not only responsible for conducting technical research but also for developing skills in entrepreneurship and public communication. As part of the challenge, the Mines team will raise a portion of their research funding through a student-led crowdfunding campaign, providing them with valuable experience in project management and public outreach.