Hildreth wins NSF CAREER Award for work to streamline post-processing in metal additive manufacturing
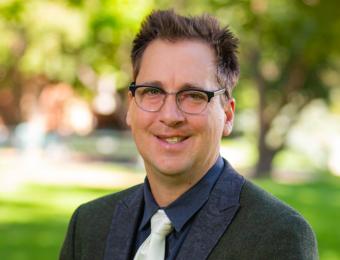
Owen Hildreth, assistant professor of mechanical engineering at Colorado School of Mines, has received a National Science Foundation CAREER Award for work that could speed the commercialization of a low-cost chemical method for the post-processing of 3D-printed metal parts.
Post-processing – the labor intensive, detailed work that must occur after an additively manufactured part is printed before it is ready for use – currently accounts for 46 percent of the cost of metal 3D printing. Overall, metal additive manufacturing is projected to be a $25 billion a year industry by 2025.
Hildreth will receive $500,000 over five years for his project, “Understanding Sensitization and Corrosion Mechanisms in Additively Manufactured Metals for Improved Surface Finish, Mechanical Properties and Corrosion Resistance.” The goal is to generate the fundamental science and understanding necessary to make chemical post-processing controllable and predictable “based on first-principle scientific understanding, instead of just knob twisting.”
Here, Hildreth answers a few questions about his research and how he’s been able to do with $3 in chemicals what a machine shop quoted him $4,000.
Q: What is your latest research focused on?
A: I developed a technology that allows you to remove a specific amount of metal off any metal surface. It has the broadest applications in 3D printing, or additive manufacturing. What we’re using it for is three purposes:
- To remove supports from 3D-printed metals – whenever you print something, there are all these support structures that anchor the part down during the printing process so it doesn’t warp from the heat. Current support removal techniques are extremely labor intensive, add significant costs and reduce design freedoms.
- Improving the surface finish – on these 3D-printed parts, the surface is really rough. Because of that roughness, if you use them in a real-world application, it can cause them to break a lot earlier than other materials. Typically, you have to do a lot of machining to smooth out the surface finish.
- With metal parts, you usually print them using powder and that powder can get stuck in channels within the parts. It’s both a health hazard – it can sometimes be explosive – and it negatively impacts the part’s performance.
Currently, all of these issues – supports, trapped powder and surface finish – add a lot of cost to the manufacturing process. Depending on the part, this post-processing could account for 20 to 76 percent of the cost of a 3D-printed part, with the average around 46 percent. With metals additive manufacturing projected to be a $25 billion business, that means they’re spending $12 billion to $14 billion a year just in post-processing. The technology I’ve developed allows us to use simple chemical techniques for all three, all in one go, and reduces post-processing costs 80-90 percent. It could be $10 billion in savings or more by 2025.
The process needs to be extremely predictable and consistent in order to transition the technology from the lab to a company. Whatever company is commercializing it needs to know how process inputs, such as etchant composition and voltage, impact process outputs, such as material removal and surface roughness. With this knowledge, processes can be designed for specific applications and with predictable results. The NSF CAREER proposal is designed to generate the fundamental science and understanding necessary to make this process controllable. What we’re specifically looking at is the sensitization and etching steps and how 3D-printed metals are different compared to traditionally processed metals.
Q: What do you find most exciting about your research?
A: For me, the most exciting part is the potential for societal impact. I’ve done a lot of science that I’ve found really interesting with immediate impacts in other scientific fields and then 20 years later, it impacts people in ways I hadn't anticipated. This is the first project I’ve had where the impact is immediate to society and the country. Over 40 companies have contacted me about the technology over the last couple of years – it’s solving a specific problem that they thought was unsolvable.
By reducing these high post-processing costs, we’re enabling American manufacturers to manufacture locally. We're enabling them to expand the design space – right now, there’s a lot of things they want to 3D-print but they don’t or can’t because they can’t remove the supports or remove the trapped powder. We’re really enabling the idea that 3D printing can create anything by eliminating the post-processing burden.
The current go-to standard for removing these supports is pliers and Dremels. If it’s a high-performance part, then they upgrade to six-axis C&C machining. All of these routes are very labor intensive. The process I’ve developed is really simple from a user standpoint. You dip your part in a sensitizing agent, you put it in a furnace, you pull it out, you put it in another chemical bath, you press a button, give it some time and it’s done. You don’t have to do a lot extra, especially compared to grinding off the supports. As an example, I made these interlocking rings. They cost $400 to print and a machine shop quoted me $4,000 to machine off the supports. I can do the same with $3 in chemicals.
Q: What is the potential impact of this work?
A: The less labor impacts where you print and where you do the post-processing, it changes the economics. Currently, a 3D-printed part has to be not only a similar cost and performance but better cost and performance.
As far as the types of parts it enables, surface finishes are a really big consideration for 3D-printed parts right now. Currently, the go-to strategy is machining the surfaces. As a result, the 3D-printed parts are near net shape, printed in close to the shape, and then you machine the rest of it. That means the part has to be machinable and that’s a limitation on what those shapes can be.
One of the things that’s generating a lot of interest is rocket nozzles – companies like Blue Origin and SpaceX are 3D-printing nozzles for their rockets. They want to be able to 3D-print cooling channels to make them more efficient. Having an etching process that removes surface roughness and any trapped powder would allow for more complicated channels and better performance from their rockets at lower cost.
Q: How does this research agenda inform your teaching?
A: I’m going to be developing a course on corrosion of additively manufactured metals. It’s going to be a hands-on lab course, which is pretty unique. A lot of times, you read about corrosion and you study it, but it is easier to understand the phenomena involved if you’ve collected and analyzed your own data. This is important because there is a lot of interest in additive manufacturing and, for these materials to be useful, we need people who understand what the corrosion response of this material is and how to evaluate it.
The other thing I’m doing is working with Corinne Packard and Ryan Richards and the Rocky Mountain Dyslexia Camp. I’ll be making modules for 3D printing and corrosion – it’s going to involve a lot of candy. We’ll show how if you have big grains, you have this kind of wicking, how grain size impacts diffusion and things like that.
We’re also sponsoring undergraduate research for computer science field sessions. It’s a pet project of mine – we’re going to be rewriting the whole communication background that is used to control scientific equipment in Swift, so your iPhone or iPad or Mac computer can control lab instruments. Tons of people know Swift – we’re hoping it enables machine equipment manufacturers and scientists to write really complex software to control their instruments without having to rely on LabView and all the costs and hassle associated with that.