Mines researchers get $2M from NASA to advance technology for extracting aluminum from lunar soil
Molten regolith electrolysis – which processes melted lunar soil to extract the metals within – is one of the leading processes for in situ resource utilization of lunar metals and oxygen
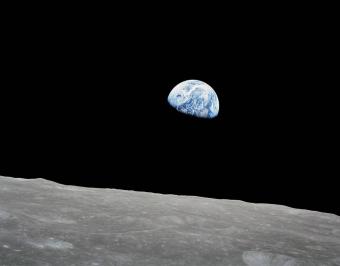
The cost to transport materials to the Moon from Earth is about $1 million per kilogram. Here, Earth is seen from the Moon in one of the iconic "earthrise" photos taken during the Apollo 8 mission. (Photo courtesy of NASA)
If humans are going to establish a long-term presence on the Moon, they’ll need resources – and more than just water and oxygen.
They’ll need metals, minerals and other materials sourced not only from Earth but also the lunar surface itself.
“It’s so expensive to land materials on the Moon if you’re bringing them from Earth,” said Kevin Cannon, assistant professor of geology and geological engineering at Colorado School of Mines. “The cost to get anything down to the Moon is about $1 million – per kilogram.”
“But if you can just bring the factory, so to speak, and source all the raw materials from the Moon’s surface, you would eventually save on the cost of what you need to bring from Earth.”
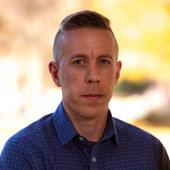
Cannon is leading an interdisciplinary team of Mines researchers that recently received $2 million in NASA funding to advance technology for the extraction of one of the more bountiful metals found in lunar soil, or regolith: aluminum.
The Mines team is focused on molten regolith electrolysis (MRE), one of the leading processes for extracting oxygen and metal from the lunar regolith.
“Essentially what we do is completely melt the regolith, turn it into a lava and electrolyze it to strip out the aluminum,” Cannon said.
With the funding from NASA, the Mines researchers will develop a tapping system that can siphon off the molten metals from the MRE reactor. That system will be integrated with an aluminum-refinement reactor and a wire-casting system to create high-purity aluminum wire that could be used as a feedstock for additive manufacturing on the surface of the Moon.
“Aluminum is commonly used on Earth in many different applications. On the Moon, we’d be interested in power transmission lines – if we wanted to collect solar power and create a grid, aluminum is one of the best materials for that – and we could also use it to make solar panel frames or spacecraft parts. It’s a very versatile metal and there’s a lot of it on the Moon, but it takes a lot of energy to liberate it.”
One of the key questions the researchers hope to answer is material compatibility. In order to function on the Moon, the reactor will need to be made of a material that can withstand the extreme temperatures required to melt the regolith, keep its strength and not get corroded by the lava.
That’s where the expertise of Mines’ Metallurgical and Materials Engineering faculty come in, Cannon said. Collaborating on the project are Associate Professor Zhenzhen Yu, Assistant Professor Jihye Kim and Associate Professor Geoff Brennecka, as well as Mechanical Engineering Professors of Practice Craig Brice (additive manufacturing) and Chris Dreyer (space resources).
Industry partner Lunar Resources will provide the MRE reactors and casting technology for turning the extracted molten aluminum metal into a wire. The two-year project will culminate in end-to-end testing at Lunar Resources’ Texas facility.
“Lunar Resources is thrilled to continue our partnership with Colorado School of Mines to jointly demonstrate the production of metal additive manufacturing wire produced from lunar regolith simulant by our industry leading ISRU technologies,” said Elliot Carol, CEO of Lunar Resources. “This program will be the first to show the potential for metallic structures and parts to be additively manufactured on the Moon with in-situ metals, a key condition for America and humanity to establish a permanent lunar presence.”