Space Resources students take second, third place in NASA Break the Ice Challenge
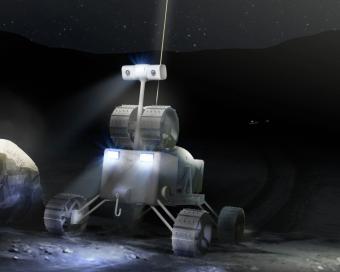
The Lunar Ice Digging System, or LIDS, would include an excavator, regolith hauler and water hauler, along with a communications and navigation system.
How can NASA effectively excavate and transport the frozen water ice on the Moon’s poles for use during upcoming long-duration lunar missions?
That’s the question the space agency posed in its latest Centennial Challenge, Break the Ice, and design solutions developed by students, faculty and alumni of the Space Resources Program at Colorado School of Mines nearly swept the awards podium.
Coming in second place – and winning $75,000 – was a team of Mines graduate students and recent alumni led by Professor of Practice George Sowers.
Winning third place and $50,000 was Austere Engineering of Littleton, Colorado, a technology startup led by students in the Space Resources Program, for its Grading and Rotating for Water Located in Excavated Regolith (GROWLER) system.
“For Mines to win the medal count really cements our position in this industry,” said Sowers, one of the core instructors in the Space Resources Program and former chief scientist at United Launch Alliance. “The team that won the overall prize was a pretty large aerospace corporation – we had graduate students that went toe to toe with a professional company.”
To tackle the challenge of in-situ water excavation and utilization on the Moon, the Mines team proposed a system made up of three rovers. The Lunar Ice Digging System, or LIDS, would include an excavator, regolith hauler and water hauler, along with a communications and navigation system.
Both haulers would have robotic arms for assembly, maintenance and repairs. All three would be remotely operated from a nearby lunar surface base or gateway.
“There are a lot of different concepts out there. Ours was heavily based on the traditional way you’d mine on Earth – using special purpose vehicles. At a strip mine, you have vehicles that each do different jobs,” Sowers said. “We also looked to minimize the mass and power consumption of these vehicles.”
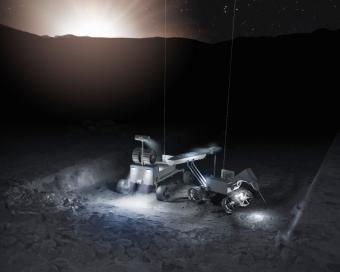
The haulers’ robotic arms were in direct response to the history of space flight and, as Sowers described, “how rovers die.” One Mars rover, for example, had to end its mission because it got stuck in deep sand and couldn’t free itself, something the hooks and winches on the two haulers would help prevent.
“We also included the ability to change wheels and other hardware parts, because experience at real mines sites on Earth is that things break all the time. It’s a dirty, harsh environment and it’s hard to keep machines running,” Sowers said.
Mines students and alumni did all the computer-assisted design work, detail design, excavation planning and route mapping for the LIDS project.
A total of 12 Space Resources graduate students and recent alumni volunteered their time and expertise: PhD students Timofey Broslav, Hunter Danque, Elizabeth Engeldrum, Michael Forlife and David Purcell; M.S. students Joseph Kenrick, Eric Luken, Matthew Rehberg and Maxwell Sissman; and recent graduates Adam Hugo MS ‘20, Ben Pemble ‘19 MS ‘20, and Deep Joshi, PhD ‘21 Petroleum Engineering. Also advising the team were Christopher Dreyer, assistant research professor in space resources, and Kevin Cannon, assistant professor of geology and geological engineering.
Joseph Kenrick started the Space Resources master's program in January and soon found himself helping with the rovers’ concept of operations and the simulation and analysis needed to determine the optimal design and parameters for the excavator, including the jackhammer.
It was the perfect project for the recent alum. Kenrick graduated from Mines in 2017 with a bachelor’s degree in petroleum engineering and worked in the oil and gas industry for three and a half years before returning to Mines to pursue his interest in the aerospace industry.
“I always thought space was what I wanted to do, but making a leap straight from petroleum to aerospace engineering, where you’re working on rockets, seemed like a pretty big leap. But the Space Resources Program is a really good bridge,” he said. “I was in a terrestrial resource extraction industry and now I’m moving into space resources extraction.”
The newness of the industry just adds “another level of excitement and technical challenge,” he said.
“There’s no set way to do things because we haven’t done it yet,” Kenrick said. “Our solution was actually quite simple – it’s a jackhammer with a bucket scoop, something that many people are familiar with. We tried to keep it simple and not do anything fancy because more complexity when you are hundreds of thousands of miles away, with no hands on it, ultimately means less reliability.”
The team’s $75,000 prize will go toward competing in Phase II of the NASA challenge, which has not yet been announced but would focus on developing and demonstrating a workable prototype of the system. Kenrick plans to stay involved.
“That’s the most exciting part for me,” he said. “A lot of what I’ve done in the past is analysis and coding, and I’ve had less experience with hands-on building and development. Being able to get that experience is invaluable and really exciting to actually build something and see how some of our analysis pans out.”